Our Team
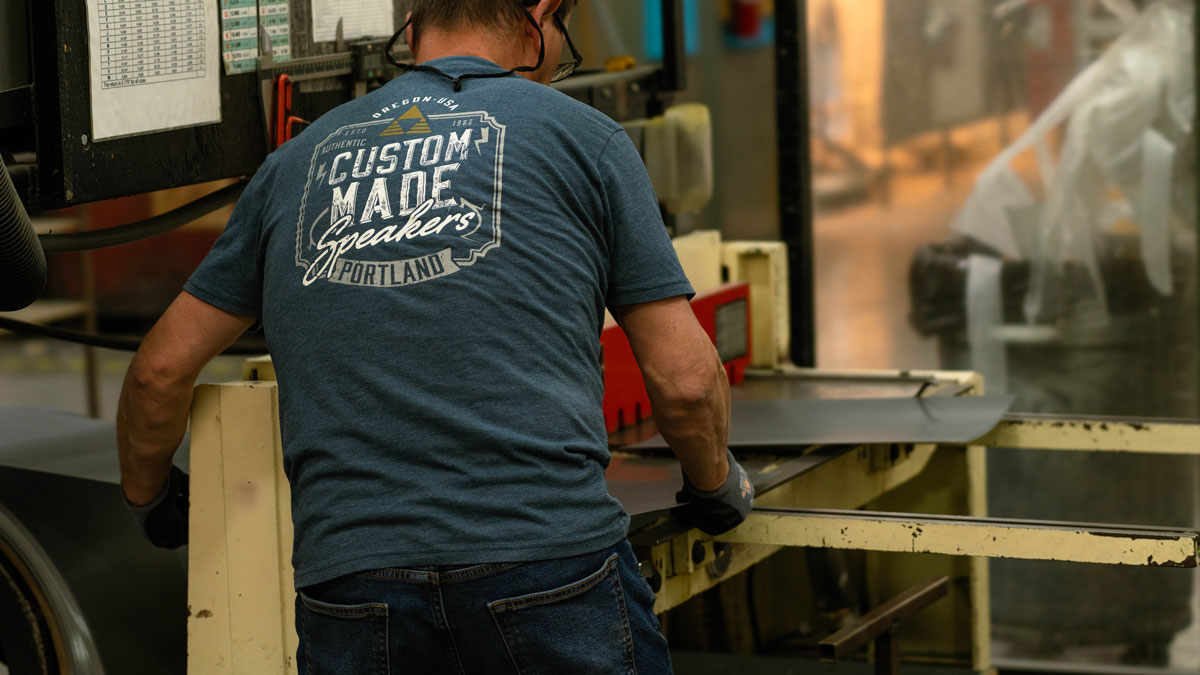
At Triad, our excellence is rooted in the passion and precision of real people who bring our products to life. With decades upon decades of professional expertise and a commitment to doing work they can be proud of, our team takes great care in every detail of product development and production, because like you, we care about the listening experience and sharing art with those we love. We invite you to meet some of our team members and learn more about how their work contributes to your finished product, and the experiences those products make possible.
Acoustical Engineer
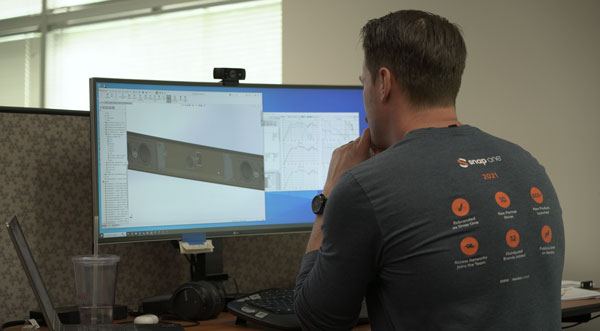
In our Engineering Department, Casey's team designs each individual speaker driver in-house using acoustic simulation software, physical prototyping, and our anechoic chamber, finalizing the crossover and the speaker’s sound. Triad is one of the few speaker manufacturers in the US with an in-house anechoic chamber, allowing us to test these components relentlessly to ensure their performance, quality and sound is perfect for every single application, delivering the experience Triad customers deserve.
Mechanical Engineer
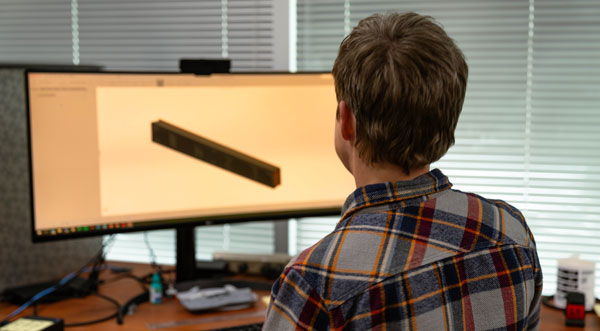
In our Design Department, Steph designs our speaker enclosures, which includes the CNC-cut MDF, custom-designed injection-molded components, and anything that goes in or on the speaker itself. The mechanical engineering team not only designs the speaker cabinets, but they CAD, CAM and prototype all their own designs and test full enclosures at every step of the way to deliver robust products that stand the test of time.
System Designer
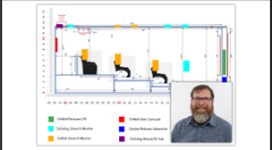
David and the Triad Design Services team work with our Triad Authorized Dealers worldwide to bring your vision to life. For any scale of home theater or whole-home listening system, a myriad of options and factors must be considered, ranging from room size and elements, to interior design, to existing and future system integration, and much more. Our Design Services team brings decades of experience to every project, tackling challenges and making dreams come true. Learn more.
CNC Specialist
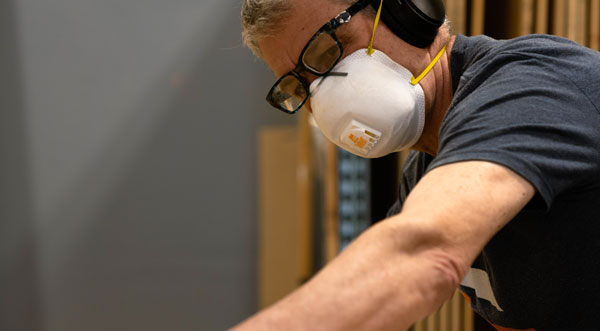
When an order is received, Leo gets to work on the production process. Triad is a built-to-order manufacturing facility, which means we can start work immediately when an order comes in. Our CNC department kicks off the production process by cutting the appropriate blank MDF from our flat stock, and then runs the specific program to cut the enclosure (or cabinet) for the product, ensuring a perfect cut for a perfect fit later in build. All of the MDF waste and dust from this department is collected and recycled by our team to reduce environment impacts and maintain a clean, safe facility.
Build Specialist
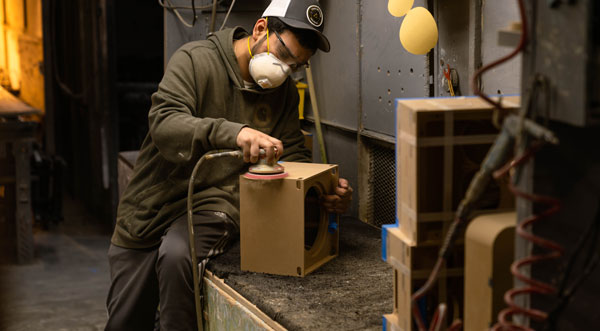
When CNC’d MDF arrives in the Build Department, Geo gets to work building the cabinets that will house internal speaker componentry. Cabinets are glued together, sanded, and filled to ensure the enclosure will have a proper air seal at the end of the line. Our team works diligently to build with precision and attention to detail, so the rest of the manufacturing process goes smoothly, and other departments can complete the build with confidence. We use water-based glues to be mindful of the environment and our team’s health and safety.
Finishing Specialist
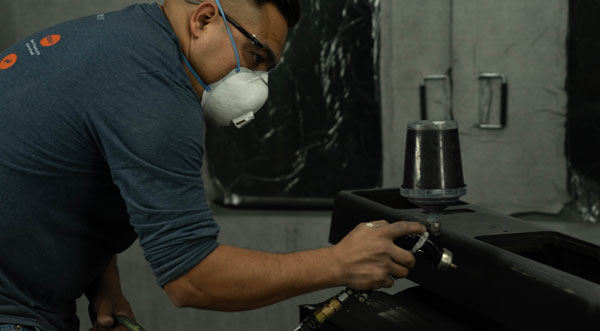
Joel custom finishes each hand-built Triad product for its unique customer. Whether a product is painted or finished with real wood veneer, our team delivers a beautiful, high-end look without compromise. Our veneer craftspeople hand-make each veneer piece that comes from our shop. We only use high-quality real-wood veneer and can match many veneers to please interiors designers and homeowners alike. We can paint match to just about any color, and the new generation of Triad products are painted in our brand-new dust-free paint booths to ensure the best finish possible.
Grille Fabricator
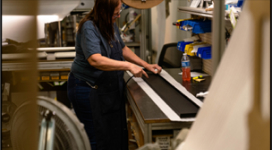
Carol puts the finishing touch on the front of our speakers, fabricating our speaker grilles in-house. For metal grilles, our team expertly cuts and bends perforated metal from bulk spools, then custom paints them if requested. Fabric grilles are hand-cut by our team and stretched over perfect-fit frames, using fabric that has a high acoustic transparency and beautiful aesthetics - never sacrificing form or function.
Assembly & Testing Expert
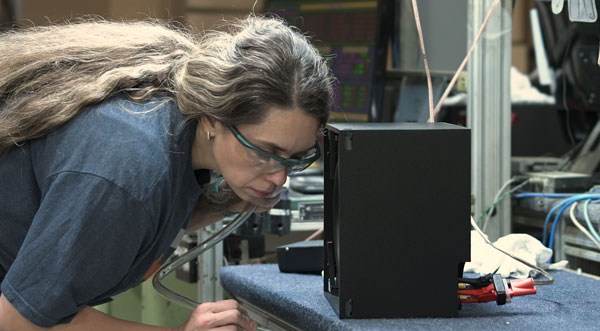
Once finishing is complete, the team moves the product to Final Assembly where Tatyana installs, wires and tests crossovers and drivers. Every speaker leaves this department having been rigorously tested to ensure it will deliver the world-renowned Triad sound. Our testing team combines technology with human expertise by leveraging acoustic testing chambers and other digital testing tools to identify things like voicing inconsistencies, air leaks, and more, then uses their passion and precision to address the issues and optimize the product.
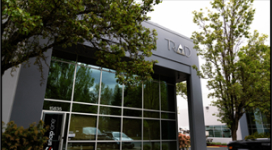
Once the product has been customized and optimized for its new home by the dedicated team at Triad, we carefully wrap and pack it in a special material and shipping box with foam inserts – all specific to the individual product - to ensure the speaker will arrive intact and as perfect as when it left the factory. From initial development to final send-off, our passionate team of experts uses the greatest care to ensure your product exceeds your expectations.
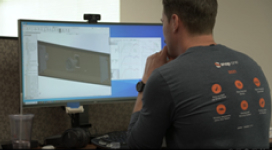
In our Engineering Department, Casey's team designs each individual speaker driver in-house using acoustic simulation software, physical prototyping, and our anechoic chamber, finalizing the crossover and the speaker’s sound. Triad is one of the few speaker manufacturers in the US with an in-house anechoic chamber, allowing us to test these components relentlessly to ensure their performance, quality and sound is perfect for every single application, delivering the experience Triad customers deserve.
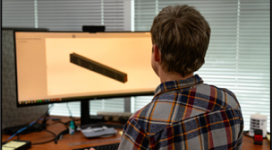
In our Design Department, Steph designs our speaker enclosures, which includes the CNC-cut MDF, custom-designed injection-molded components, and anything that goes in or on the speaker itself. The mechanical engineering team not only designs the speaker cabinets, but they CAD, CAM and prototype all their own designs and test full enclosures at every step of the way to deliver robust products that stand the test of time.
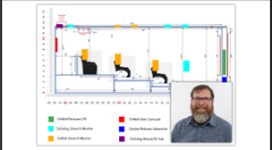
David and the Triad Design Services team work with our Triad Authorized Dealers worldwide to bring your vision to life. For any scale of home theater or whole-home listening system, a myriad of options and factors must be considered, ranging from room size and elements, to interior design, to existing and future system integration, and much more. Our Design Services team brings decades of experience to every project, tackling challenges and making dreams come true. Learn more. (hyperlink to end-user facing Design Services page)
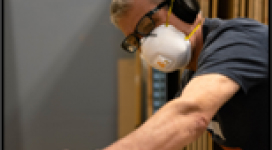
When an order is received, Leo gets to work on the production process. Triad is a built-to-order manufacturing facility, which means we can start work immediately when an order comes in. Our CNC department kicks off the production process by cutting the appropriate blank MDF from our flat stock, and then runs the specific program to cut the enclosure (or cabinet) for the product, ensuring a perfect cut for a perfect fit later in build. All of the MDF waste and dust from this department is collected and recycled by our team to reduce environment impacts and maintain a clean, safe facility.
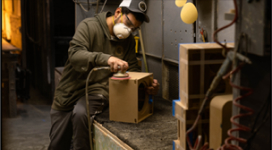
When CNC’d MDF arrives in the Build Department, Geo gets to work building the cabinets that will house internal speaker componentry. Cabinets are glued together, sanded, and filled to ensure the enclosure will have a proper air seal at the end of the line. Our team works diligently to build with precision and attention to detail, so the rest of the manufacturing process goes smoothly, and other departments can complete the build with confidence. We use water-based glues to be mindful of the environment and our team’s health and safety.
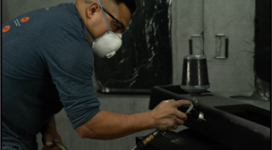
Joel custom finishes each hand-built Triad product for its unique customer. Whether a product is painted or finished with real wood veneer, our team delivers a beautiful, high-end look without compromise. Our veneer craftspeople hand-make each veneer piece that comes from our shop. We only use high-quality real-wood veneer and can match many veneers to please interiors designers and homeowners alike. We can paint match to just about any color, and the new generation of Triad products are painted in our brand-new dust-free paint booths to ensure the best finish possible.
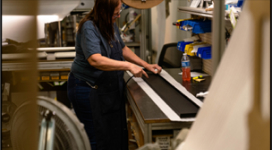
Carol puts the finishing touch on the front of our speakers, fabricating our speaker grilles in-house. For metal grilles, our team expertly cuts and bends perforated metal from bulk spools, then custom paints them if requested. Fabric grilles are hand-cut by our team and stretched over perfect-fit frames, using fabric that has a high acoustic transparency and beautiful aesthetics - never sacrificing form or function.
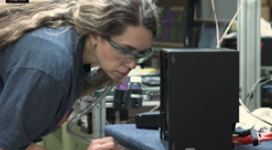
Once finishing is complete, the team moves the product to Final Assembly where Tatyana installs, wires and tests crossovers and drivers. Every speaker leaves this department having been rigorously tested to ensure it will deliver the world-renowned Triad sound. Our testing team combines technology with human expertise by leveraging acoustic testing chambers and other digital testing tools to identify things like voicing inconsistencies, air leaks, and more, then uses their passion and precision to address the issues and optimize the product.AWAITING IMAGE – NEED STILL FROM VIDEO FOOTAGE
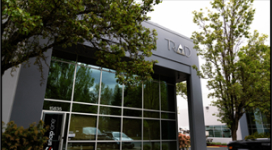
Once the product has been customized and optimized for its new home by the dedicated team at Triad, we carefully wrap and pack it in a special material and shipping box with foam inserts – all specific to the individual product - to ensure the speaker will arrive intact and as perfect as when it left the factory. From initial development to final send-off, our passionate team of experts uses the greatest care to ensure your product exceeds your expectations.